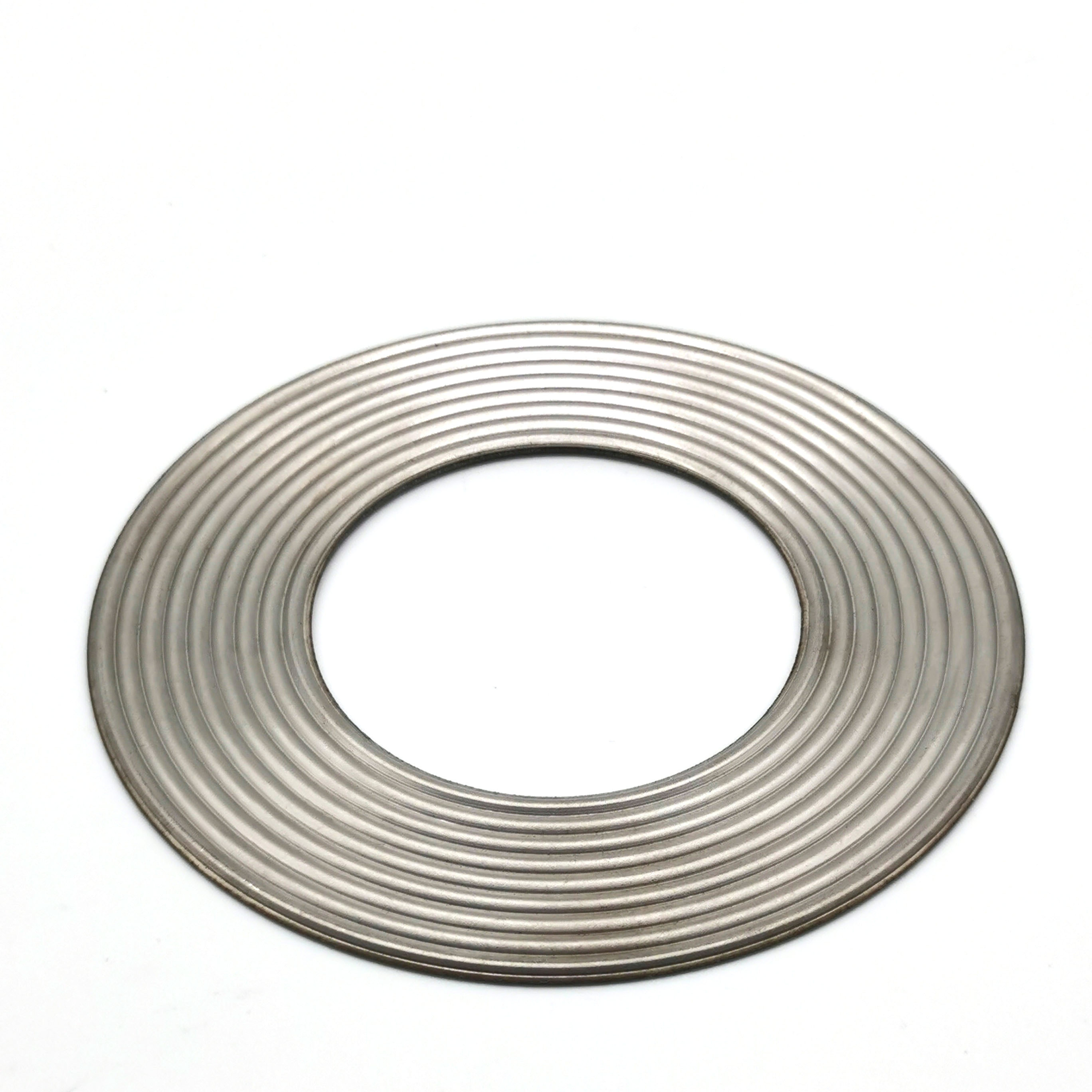
Custom Corrugated Gasket
The corrugated metal gaskets can be direct replacements for spiral wound gaskets. It can eliminate inward buckling issues while creating a seal at moderate flange stresses.
Corrugated metal is covered with graphite, ceramic, or PTFE layer. An additional finishing layer is applied depending on the requirements of the medium to be sealed. The gaskets with a soft layer on both sides are used in low-pressure applications in large diameter flue gas ducts at high temperatures
Available in a wide range of substrate alloys and covering layer options. Corrugated flange gaskets can be utilized to solve many common flange problems.
They have been proven to be both reliable and cost-effective for the application on flanges and heads where boat loading is sufficient.
Temperature Min Max, in air Max, in steam |
-200C(-328F) 454C(850F) 650C(1,200F) |
Pressure, max, bar (psi) | 207 (3,000) |
PH range, room temp | 0~14 |
Gasket Factors Gb, psi (Mpa) a Gs, psi |
575 (3.84) 0.325 2.21 |
Dimensions for Corrugated Metal Gaskets to Suit ASME B16.5 Flanges
CLASS | 150# | 300# | |
NPS | ID | OD | OD |
1/2″ | 0.84 | 1.88 | 2.12 |
3/4″ | 1.06 | 2.25 | 2.62 |
1″ | 1.31 | 2.62 | 2.88 |
1-1/4″ | 1.66 | 3.00 | 3.25 |
1-1/2″ | 1.91 | 3.38 | 3.75 |
2″ | 2.38 | 4.12 | 4.38 |
2-1/2″ | 2.88 | 4.88 | 5.12 |
3″ | 3.5 | 5.38 | 5.88 |
3-1/2″ | 4.00 | 6.38 | 6.50 |
4″ | 4.50 | 6.88 | 7.12 |
5″ | 5.56 | 7.75 | 8.50 |
6″ | 6.62 | 8.75 | 9.88 |
8″ | 8.62 | 11.00 | 12.12 |
10″ | 10.75 | 13.38 | 14.25 |
12″ | 12.75 | 16.13 | 16.62 |
14″ | 14.00 | 17.75 | 19.12 |
16″ | 16.00 | 20.25 | 21.25 |
18″ | 18.00 | 21.62 | 23.50 |
20″ | 20.00 | 23.88 | 25.75 |
24″ | 24.00 | 28.25 | 30.50 |
Tolerance:
- OD: 1/2″~12″ = +0~-0.063″, 14″~24″ = +0~-0.125″
- ID: 1/2″~12″ = +/-0.063″, 14″~24″ = +/- 0.125″
Corrugated Gasket Manufacturers FAQ
Corrugated Gasket FAQ Guide
Corrugated gaskets are the gaskets we often see in heat exchangers where we see a lot of radial shears. Generally, we recommend Kammprofile gaskets for heat exchanger applications, but due to the high usage we see in applications, we will cover the details of corrugated gaskets.
[lwptoc skipHeadingLevel=”h1,h3,h4,h5″ skipHeadingText=”*Custom Corrugated Gasket|*Corrugated Gasket Manufacturers FAQ|*Request Your Free Corrugated Gasket Quote Today|*Corrugated Gasket FAQ Guide”]
1. What is a Corrugated Gasket?
Corrugated gaskets can be used for special flanges such as heat exchangers. Nonetheless, the corrugated gaskets should not be used on pipe flanges (standard ANSI flanges) without proper engineering consideration. Even with engineering considerations in mind, we still recommend using better sealing products such as spiral wound gaskets or kammprofile gaskets instead of corrugated gaskets!
They are sheet metal from which the manufacturer makes a corrugated metal core. Gaskets should be used with a soft side, which basically means flexible graphite (that’s what the gasket company calls it, and we call it graphite), or another filler material on each side, like PTFE.
Corrugated metal cores can be made from conventional gasket materials such as carbon steel, 304 stainless steel, 316 stainless steel (if you need to go to higher temperatures), and other high-temperature materials.
Filler materials usually have a graphite face layer. Other non-asbestos fillers can accommodate this gasket, but in petrochemical applications, we only see graphite finishes.
While we are less familiar with the use of corrugated metal gaskets outside of petrochemical applications, many companies say these gaskets are also made from compressible sealing elements designed to resist high temperatures, aggressive chemicals, and thermal cycling.
NOTE: We will not discuss – Ring Joint Gaskets (RTJ), Elastomeric Gaskets, Compression Packing, O-Rings, Gaskets, and Plain Graphite Gaskets.
2. Where is a Corrugated Gasket not used?
Spiral wound gaskets are preferable to corrugated gaskets for pipe flanges. These applications are not a good idea, especially with ASME B16.5 flanges.
Due to their lack of thermal resistance, they are not considered superior sealing products. This is because recovery in spiral wound gaskets is better for pipe flanges, and a corrugated gasket is not commonly used as a sealing product for these flanges.
There have been papers on how graphite sealing elements can burst when thermally cycled and have not recovered. With spiral wound gaskets, the graphite sealing element fills in between the windings and has a better chance of resealing the flange.
3. What is the best use for a corrugated gasket?
We see corrugated gaskets and kammprofile gaskets in heat exchangers and some expansion joints in petrochemical applications. corrugated gaskets are suitable for heat exchangers and expansion joints because they are good at resisting free radical shear and have some compressibility and recovery.
They will be an upgrade to double jacketed gaskets, but most petrochemical sites will standardize kammprofile gaskets as their specially selected heat exchanger.
We see these applied to exchangers because of their good radial shear due to their compressibility and recovery due to flexible graphite.
These are suitable for high-temperature and high-pressure exchangers as they can withstand 45ksi gasket stress. Of course, you’ll need to calculate the bolt loads using ASME PCC-1 Appendix O to make sure you don’t overstress these washers.
When double-jacketed gaskets are the gasket of choice for heat exchangers, corrugated gaskets can fill in the gaps well because kammprofile gaskets are so expensive. Since then, manufacturers have done a good job of reducing the price of kammprofile gaskets over the past 20 years so that the price difference between them and CMG is negligible. Today, we are seeing less and less use of CMG due to kammprofiles.
4. Reasons for choosing corrugated gaskets instead of spiral wound gaskets
Corrugated gaskets are an excellent alternative to spiral wound gaskets. In spiral wound gaskets, strips of gasket material are rolled into rings and placed between flanges. Spiral wound gasket manufacturers in India supply these sealants to food processing, power, pharmaceutical, petrochemical, shipbuilding, and other industries. What is the advantage of corrugated gaskets over spiral wound gaskets? Let’s find out.
- structure
Spiral wound gaskets usually have an inner ring or centering ring, and a filler material made of PTFE or graphite. The inner ring provides robustness and the outer ring acts to center the gasket between the flanges. Spiral wound gaskets are used in high-pressure environments with extreme operating conditions. High-performance spiral wound gasket models can withstand pressures up to 320 bar.
The construction of a corrugated gasket consists of a metal core and sealing elements for extreme environments. They are made of corrugated stainless steel rings with layers of soft material such as PTFE or graphite on both sides. The gasket can withstand pressures up to 160 bar.
Depending on the application, corrugated gaskets can be manufactured in different shapes such as round, rectangular, oval/oval, or custom shapes. Typically, heat exchangers require gaskets with custom construction. To meet such requirements; corrugated gasket manufacturers can design custom corrugated gaskets as needed.
- Performance
Corrugated gaskets are more marketable than traditional gasket designs. These gaskets are perfect for older plants and equipment. Use corrugated gaskets to increase resistance to radial shear and thermal cycling. Additionally, corrugated gaskets function effectively at low seat stress levels.
Spiral wound gaskets with graphite fillers can withstand temperatures as low as -200 degrees Celsius or as high as 550 degrees Celsius. Likewise, corrugated gaskets can resist temperatures as low as -200 degrees Celsius and as high as +450 degrees Celsius. Corrugated gaskets with a mica layer are available for operating temperatures greater than or equal to 550 degrees Celsius.
- Application
Corrugated gaskets are ideal for challenging environments where gas, oil, chemicals, acids, and more are handled. With this type of spacer, you get excellent elasticity and recovery. Additionally, well-known corrugated gasket manufacturers manufacture premium gaskets to ensure higher sealing and less slack for better stability and handling.
You can find spiral wound gaskets in heat exchangers, pumps, valves, boilers, manhole covers, compressors, and more. Corrugated gaskets are an excellent choice for harsh environments involving valve, steam, pressure vessel, gas, and heat exchanger applications. In addition, these gaskets can provide high performance in pipelines, nuclear power plants, and conventional power plants.
What makes corrugated gaskets a better alternative to spiral wound gaskets?
- Corrugated gaskets perform well at lower surface pressures compared to spiral wound gaskets.
- Corrugated gaskets work effectively when used with standard flanges. In addition, these gaskets are suitable for defective flanges. Corrugated washers are designed to work effectively on uneven flange surfaces and do not require specially designed flanges.
- Compared to spiral wound gaskets, corrugated gaskets have an inner hole design to ensure that no media contamination occurs.