Place of origin: | China |
MOQ: | 1 roll |
Production capacity : | 10tons/Month |
Delivery time: | 3-5 days generally after getting your PO |
Package: Carton. | coil per roll and then put in the carton |
Certificate: | Industry Standard, ISO9001 |
Material:P | PTFE, Graphite, Aramid, Carbon Fiber, Acrylic Fiber, Ramie Fiber, Kynol Fiber, and so on |
feature: | fluid sealing material for Pump&Valve |
Usage: | suitable solutions to increase the reliability of rotating &Reciprocating equipment and valve |
Braided packaging is a kind of material like rope, which is cut into loops and wound around rods. When the gland is tightened, radial pressure is generated as a result of the compression force. Since braided packing expands radially when compressed, the gland tolerance is more flexible than when using v-shaped packing. braided packing is also called compressed packing, gland packing, and rope packing.
It is usually produced in a square or rectangular section and is available in various materials. As a compression or rope packing, gland braided packing is a highly multipurpose sealing solution for pumps, valves, agitators, and other rotary equipment
Longseal gland braided packaging includes almost all sealing packing types. We provide regular products, and can also provide OEM braided packings according to customer needs. From raw materials to finished products, we strictly control every aspect of production. Provide reliable gland braided packing. For a quote, please contact one of our sealing professionals.
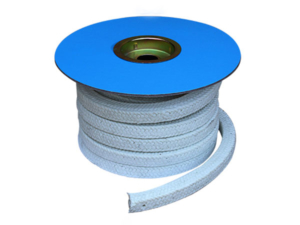
Acrylic PTFE Packing
Acrylic PTFE Packing is braided from high strength acrylic synthetic yarns with PTFE impregnated twice. The Acrylic PTFE packing has excellent properties of tightness, lubricity, and good resistance to chemicals. Wide variety of uses throughout a plant. Used in pumps and valves, it can handle most chemicals except strong acid, strong alkali, and a strong oxidizer. Especially for the condition of middle temperature, high pressure, high speed, and where contamination is not permitted.
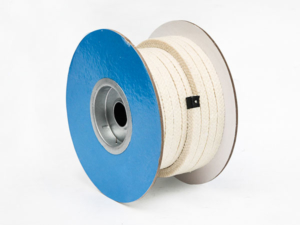
Aramid PTFE Packing
Aramid PTFE Packing braided from high-quality Dupont Aramid /Kevlar yarns which are uniformly impregnated with PTFE dispersion. The packing shows good chemical resistance, high elasticity, and very low cold flow. It is wear-resistant but may damage the shaft if not used properly.
The aramid fibre can be braided in many types for different applications, such as Aramid PTFE Packing with lubricant for a slurry service application, Spun aramid fibre packing with economical use; PTFE packing with Aramid corner, Graphite PTFE Packing with Aramid Corner, GPTFE & Aramid in Zebra braided packing, etc.
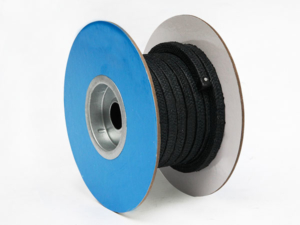
Carbonized Fiber Packing
Carbonized fibre packing is braided from oxidized PAN fibre impregnated with PTFE, silicon-oil-free. Compared with traditional carbonized fibre packing, it is not brittle and is suitable for high peripheral speed applications.
With the high strength and good thermal conductivity of the PAN fibre, and excellent self-lubrication of the PTFE, the packing has a long life and does not damage shafts. The related carbon fibre packing for a different purpose is available, such as Carbonized fibre packing with graphite, Carbonized Fiber Packing Reinforced with Nickel wire, Carbon fibre packing.
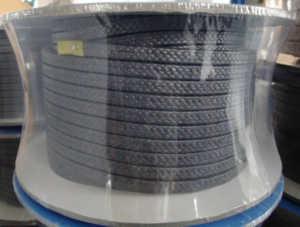
Expanded Graphite Packing
Graphite packing is braided from low-sulfur expanded graphite yarns, which are reinforced by cotton, carbon fibre, glass fibre, etc. It has very low friction, does not damage shafts or stems. It shows good thermal and chemical resistance and high elasticity. To improve mechanical strength, Graphite packing can be reinforced with Inconel wire, ss wire, nickel wire, etc metal materials.
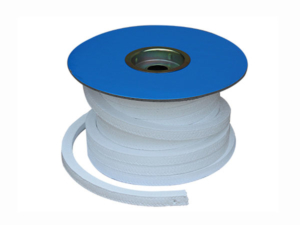
Pure PTFE Packing
Pure PTFE Packing is a pure PTFE fibre yarn braided into the square cross-section and impregnated with PTFE dispersion. High cross-sectional density and structural strength. It is designed for valves and lower shaft speed application under medial pressure in food processing, pharmaceuticals, paper mills, fibre plants where high purity and corrosion resistance is required. PTFE packing can be also treated with lubrication, it is an economic type.
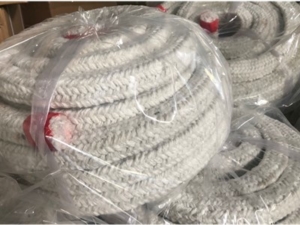
Ceramic Fiber Packing
Ceramic fibre braided packing rope is made from high-quality ceramic fibre, it has excellent capabilities of high strength and high-temperature resistance. Ceramic fibre is a standout among the different organic and inorganic fibres as an ideal replacement for asbestos, it has excellent capabilities of high strength and high-temperature resistance. Ceramic Fiber Packing can be impregnated with graphite or insert with steel wire
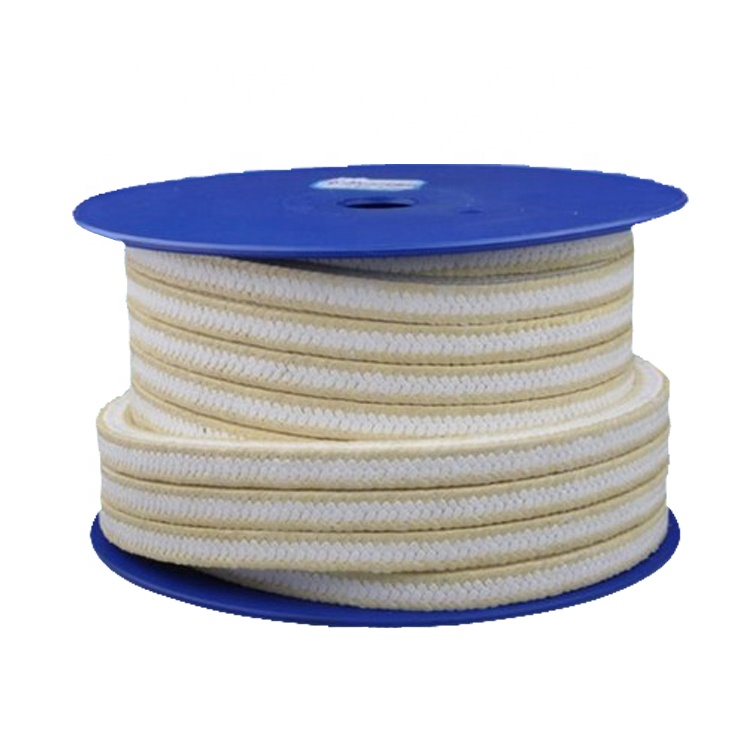
PTFE Packing With Aramid Corner
PTFE Packing with Aramid Corner is made of aramid yarns impregnated with PTFE, while the friction faces are made of pure PTFE yarns. This structure enhances the lubrication ability of aramid fiber and improves the strength of the pure PTFE. This unique multi-wire braiding technology enhances both lubricity and tensile strength, significantly extending service life in demanding applications.
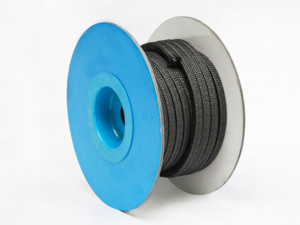
Graphite PTFE Packing
Graphite PTFE (gPTFE) braided packing, also known as Black PTFE Packing, is a high-performance sealing material made from braided PTFE yarn uniformly embedded with graphite particles. the Graphite PTFE packing can be widely used in most chemical pump applications, except for molten alkali metals, fluoride solutions, fuming nitric acid, and other strong oxidizing agents
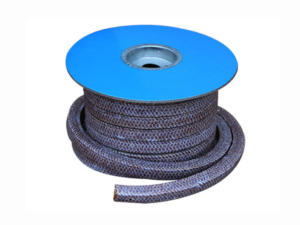
Kynol Fiber Packing
Kynol Fiber Packing Braided (GOLDEN Packing) is made with high-performance Kynol fibers, ensuring durability and reliability. The special process assures thorough lubrication for a longer Packing life. Its unique design and material combination ensure outstanding performance in high-temperature, high-pressure, and chemically corrosive environments, making it an ideal choice for pump and valve sealing.
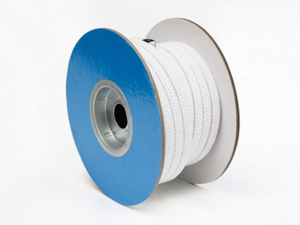
Ramie Fiber Packing
Ramie Fiber packing is made of high-quality ramie fiber, impregnated with light-colored, special PTFE, and lubricant during square plaiting operation.it is not harsh on shafts and stems. It is widely used for pumps, refinery equipment, filters, valves, etc. It is also available with Ramie fiber packing with a silicon rubber core,high-elasticity silicone core absorbs vibration, improves sealing, and controls leakage.
Braided Packing Manufacturers FAQ
Braided Packing – Definitive Guide
Braided packing is also called compression packing, gland packing or rope packing. It is a sealing device in mechanical equipment. It performs a sealing function and usually controls fluid or gas leakage. Braided packing is usually made of relatively soft and flexible material and consists of many rings inserted into the annular space (stuffing box) between the rotating or reciprocating component and the pump or valve body.
Through the follower or packing gland close to the top ring, the pressure is transmitted to the packing group, so that the packing ring is close to the side of the stuffing box and the reciprocating or rotating parts expand radially to achieve sealing.
Packing is typically woven from a variety of materials and has a square or rectangular cross-section. Compressed fillers are not only different due to their different weaving materials, but also different ways of weaving.
[lwptoc skipHeadingLevel=”h1,h3,h4,h5,h6″ skipHeadingText=”*Custom Braided Packing|*Acrylic PTFE Packing|*Aramid PTFE Packing|*Carbonized Fiber Packing|*Expanded Graphite Packing|*Pure PTFE Packing|*Ceramic Fiber Packing|*PTFE Packing With Aramid Corner|*Graphite PTFE Packing|*Kynol Fiber Packing|*Ramie Fiber Packing|*Braided Packing Manufacturers FAQ|*Request Your Free Braided Packing Quote Today|*Braided Packing – Definitive Guide”]
1. Application of Braided Packing
Woven packing is mainly used in processing industries such as petrochemical, paper and steel plants, as well as service industries such as public utilities, ocean, water supply, sewage, food and nuclear energy. They seal all types of fluids, including water, steam, acids, corrosives, solvents, gases, petroleum, gasoline and other chemicals under a wide range of temperature and pressure conditions.
These elements are a part of rotary pumps, centrifugal pumps, reciprocating pumps, as well as valves, expansion joints, soot blowers, and many other mechanical devices. Braided packing is relatively easy to install and maintain. If you pay attention to it properly, you can expect a high degree of success in the operation.
The successful sealing of compressed packing depends on several important related factors:
- Choose packing materials carefully to meet specific application requirements.
- Full consideration of surface speed, pressure, temperature and medium deal with.
- Pay due attention to good installation and break-in procedures.
- High standards of equipment maintenance.
2. Function of Braided Packing
Fluid film lubrication is provided by braided packing in pumps, regardless of whether they are rotating or reciprocating. The source of this fluid film is a built-in lubricant (liquid, solid or combination), leakage of the processing medium or external lubricant supply. When the equipment is started, the lubricating oil can be released from the packing through the gland pressure to provide initial lubrication and sealing.
During running-in, these lubricants bridge the gap between dry operation and the introduction of normal lubrication systems. Gradually, by adjusting the gland pressure, pumping medium or external lubrication source, and providing a continuous fluid film source, the lubrication function is taken over. The gland pressure is adjusted to provide the best lubrication for the seal to prevent overheating and damage to the shaft or rod.
The built-in lubricating oil is gradually lost during the operation of the equipment, which can be compensated by further adjustment of the gland. When the volume loss of the lubricating packing is close to the original amount of the built-in lubricant, the effectiveness of the packing is lost and needs to be replaced. The built-in lubricant can also play an important role in blocking the passage of the pumped liquid, thereby preventing excessive leakage.
The use of braided packing in slow or infrequent moving valves, as well as the use of braided packing in static operation, require sealing without leakage. Various impregnants can be used to assist in this function. Some fillers use non-migration stable lubricants that can work under extreme pressure and temperature.
Described below is a typical method of using compressed packing in a pump. Note that if external lubrication is required, a collar (sealed cage) should be used.
3. Braided Packing Construction
Braided packing is often used in the stuffing box of pumps to seal various types of fluids. Dama can provide woven packing of various structures, and each design can meet specific operating environment conditions. Its lineup includes square weaves, weaves on weaves, cores on weaves, and interwoven weaves, each of which is made of weaving yarns, ribbons, rovings and other materials in different ways.
1) Square braid
Square knitting (also known as square knitting) packing is to pass materials on and under the strands in the same direction. The resulting filler is usually soft and has the ability to carry large amounts of lubricant. This kind of braided packing is convenient to use on equipment. In fact, its softness makes it suitable for old and worn equipment. It is often used for high-speed spinning services with relatively low pressure. This kind of packing is usually provided in a square cross-section, but this weaving method can also produce a rectangular size.
2) Braid over braid
Sometimes referred to as circular knitting or multiple knitting, knitting packing uses a circular knitting machine to create a tubular jacket. In order to obtain the required size, these jackets are knitted piece by piece. This type of packing is relatively dense and is very suitable for high-pressure, low-speed applications, including valve stems, expansion joints, groove washers, etc. It can provide a round, square or rectangular cross-section.
3) Braid over core
Woven over-core packing is made by weaving one or more jackets on a core that can be squeezed, twisted, wound, or woven. This filler has a wide range of density and cross-section.
4) Inter-braid
Braided packing is made by crisscrossing threads through the packing body diagonally from the surface. This type of braiding provides a strong overall structure because each strand is strongly locked to the other strands. The resulting filler is relatively dense but very flexible. It has durability, evenly distributed yarn density and excellent lubricant retention. This type of packing is suitable for agitators, valves, grooves, expansion joints, reciprocating pumps and centrifugal pumps.
4. How to Install Gland Packing?
As one of the most commonly used sealing technologies, compressed packing exists in any facility or factory for pumps and valves. Improper installation or sealing can cause shaft or sleeve wear, overheating and abnormal leakage. The team must ensure that they know how to install the compressed packing and carefully follow the best practice steps. First, make sure that the correct fibre type is selected.
1) Select Fiber
Choosing the wrong filler fibre can lead to premature wear and filler failure. There are many variables in this choice. This includes understanding different fibers. Packing fibers that need to be considered are:
- flax
- Acrylic fibre
- carbon
- Aramid
- PTFE
- graphite
- Combination of multiple fibres
2) Fixed Braid Types
Different braid types are also available, including:
- Multi-lok
- Square weave
- Woven over the core
- Braid
- distortion
In addition, the packing can be used for any rotating equipment, such as pumps; valves; doors; and other equipment.
5. Step By Step to install gland packing
Here is an infographic detailing the steps to properly install and install the packing.
By following the five best practices described in this infographic, the factory team can almost eliminate excessive leaks caused by improper packing installation and will reduce equipment downtime. These best practices include:
- Choose the right fibre.
- Use the best method to install the packing correctly (use tools to ensure the ideal seat position).
- Follow appropriate maintenance recommendations.
- If your operating parameters change, please reconsider packing fibre and maintenance procedures.
- Please replace the packing when it is used up.
Extend packing and asset life
Following these guidelines on how to install compressed packing will help extend the life of the packing and the life of the rotating equipment. Remember, if any of the following parameters change, you need to reconsider packing fibres and lubrication:
- Flow
- Running time
- Working temperature and pressure
- Pumping materials (especially pH value)
6. How to avoid failure of woven packing?
Compressed packing has existed since the beginning of the industrial revolution, and is still widely used in various equipment that requires stuffing box sealing to prevent process fluids from being lost to the environment. Over time, with advanced rotary sealing solutions, such as mechanical seals, compression remains an important industrial tool.
1) Gland Pressure
Install the sleeved packing ring into the stuffing box (as shown in Figure 1) to form a compressed stuffing box seal. Then tighten the gland on the back of the stuffing box to compress the packing between the shaft and the stuffing box wall. Once compressed, the packing expands, applying a radial force to the sides and shaft of the stuffing box.
2) Stuffing box packing (graphics provided by FSA)
When the gland pressure is applied, the built-in lubricating oil is released from the packing. These lubricants are particularly important when the equipment is started. Finally, the processing fluid or external flushing fluid takes over the lubrication function of the packing and provides a continuous fluid film to reduce friction. The heat is dissipated through the shaft, packing, pump casing, and process fluid.
The built-in lubricant is gradually lost during the operation of the pump, and it is usually necessary to further adjust the gland. The gland pressure is adjusted to provide the best lubrication for the seal and prevent overheating. Over time, the loss of lubricant and the wear of the packing ring will result in a gradual decrease in effectiveness, leading to the need to replace the packing.
3) Packing Materials
The choice of packing material affects the operating cost of the centrifugal pump, but its relationship is little known. The Fluid Sealing Association (FSA) and the European Sealing Association (ESA) began to solve the problem of lack of data by developing industry-standard test methods to clarify the behaviour of fillers.
The acronym “STAMPS” can be used to remember the key considerations in deciding which packing material and structure to choose:
- Size-What is the size of the stuffing box?
- Temperature-What is the temperature of the medium?
- Application-what type of device is it?
- M medium-what medium is sealed?
- P pressure-what is the internal pressure being sealed?
- Shaft Speed-What is the surface speed of the shaft?
4) Compression Packing Failure
A common mistake is to tend to maximize the packing’s service time to a perceived point of failure and then replace it. Defining failure is more a matter of opinion than a matter of science. Signs of packing failure include increased leakage, smoke from the stuffing box, or uncontrolled gland leakage.
Safety-conscious operators regularly repair the pump and replace the packing. However, there is currently no established replacement frequency or general standards related to packing materials. The acceptable replacement cycle time largely depends on the application, equipment, and packing.
This confusion is due to the forgiving nature of compressed packing. Unless the packing fails, the operation of the pump will not be affected. It should be replaced long before this happens. For any type of packing, operating costs are relatively fixed under normal operating conditions. As the performance deteriorates, the increase in operating costs is far greater than the initial cost of the packing ring group.
Depending on how the packing works, there are three factors that affect the cost:
- Power loss, shaft/sleeve wear and material wear due to friction
- The leakage rate of external flushing fluid from the stuffing box to dissipate the heat caused by friction
- Efforts to adjust the pressure of the packing gland to keep the leakage rate of the stuffing box to a minimum
The best practice is to monitor changes to the stuffing box and replace the packing before the cost increases. There are many costs, and depending on each application, any one of them may be the most important. For example, the cost of product loss and product dilution may be much higher than power consumption or flushing water loss, depending on location and labour costs.
5) Signs of failure
When the pump and auxiliary system reach a stable state, measure the temperature at the stuffing box and record the difference with the ambient temperature. For example, if the ambient temperature is 65 degrees Fahrenheit and the stuffing box temperature is 110 degrees Fahrenheit, the working baseline difference is 45 degrees Fahrenheit.
Measure the drop rate of the stuffing box, a few drops per minute, and record it. Over time, the operator will adjust the gland follower to maintain this drip-rate. The signs of invalid packing and requiring replacement are now easier to identify and can include any of the following:
- The baseline drip rate can no longer be controlled by the normal gland follower adjustment.
- The stuffing box/ambient temperature difference is significantly increased (+ 25%) from the baseline reading when the stuffing was first installed.
- The filler is squeezed out from the rear of the pump.
- Turn off the pump for maintenance, and the packing shows that the material is hard or brittle.
Replace the packing and follow these steps to improve performance, avoid over-process fluid loss, and save money. It is no longer necessary to increase the adjustment of the gland and extend the life of the shaft/sleeve.