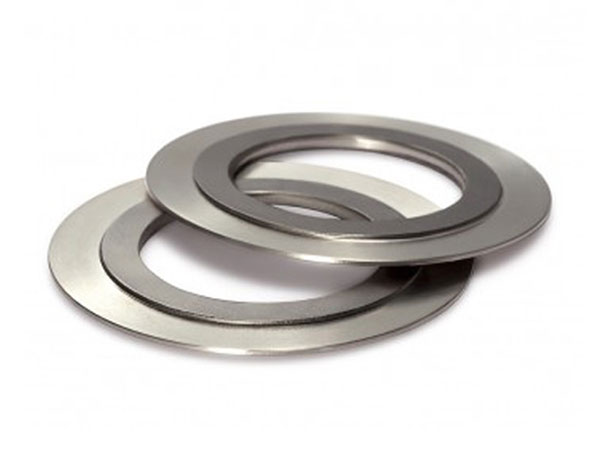
Custom Kammprofile Gasket
Kammprofile gasket consists of a concentrically serrated solid metal core with a soft conformable sealing layer bonded to each face. The layer can be expanded graphite, ptfe, asbesots free gasket sheeting material or some soft metal.
It features excellent compressibility and good recovery characteristics. The gasket mainly suits for vacuum and extremely high pressure applications. It can an be refurbished and reused and has better leak tightness than spiral wound gaskets.
It is the ideal replacement for equipment applications where standard spiral wound gaskets, double jacketed gasket, and corrugated metallic gaskets are commonly used.
It improves performance at low seating stresses and particularly suits applications where high temperatures, pressures, and fluctuating conditions are encountered.
GS003a Kammprofile gasket basic style
the basic gasket without the inner and outer ring.
GS003b Kammprofile gasket with the integral outer ring
It is with a machined centering ring that ensures optimum gasket positioning between the bolts.
GS003c Kammprofile gasket with the loose outer ring
This type of gasket suits nominal pipe size and pressure class raised face flanges.
Material | Thick (mm) | Density(g/cm3) | Hardness(HB) | Temperature(°C) |
CS/SoftIron | 2 | 7.85 | 90~120 | -60°C~+500 |
SS304,SS304L | 3 | 7.9 | 130~180 | -250°C~+550 |
SS316,SS316L | 4 | 7.9 | 130~180 | -100°C~+550 |
Kammprofile Gasket Manufacturers FAQ
1. What is a kammprofile gasket?
Kammprofile gaskets are gaskets that feature a metal core bonded with soft filler material on both sides. After the Kammprofile gasket is installed, the soft non-metallic filler is pushed into the metal core serrated groove.
2. What material is the kammprofile gasket made of?
The kammprofile gasket is made of a solid metal core and can be used with conventional gasket materials. The materials include carbon steel, 304 stainless steel, 316 stainless steel (for higher temperatures), and other high-temperature materials such as Hastelloy and Inconel.
Gaskets manufacturers would make the metal into the shape that looks like grooves and put it into the gasket material; this is where our term grooved metal gaskets come from. These metals are made to place a facing material on the sealing surface.
The facing material (filler material) is usually a soft facing material such as graphite facing (flexible graphite is what the manufacturer calls it). Other non-asbestos fillers include mica (for high-temperature applications), Teflon, and other sealing materials.
While they don’t require guide rings (like the outer ring of a spiral wound gasket), we like to see them on the gasket as this helps center the gasket during assembly. This could accommodate this gasket, but we’ve only seen graphite faces in petrochemical applications.
3. What are the key features of kammprofile Gaskets?
The key features of kammprofile gaskets include:
- Provide high integrity sealable to withstand thermo-cycling and shock-loading conditions
- Insufficient bolt load prevents conventional gasket materials from sealing
- Widely applicable
- Flanges are protected by the soft facing layer
- Refurbished with a new facing layer and reused
- Uneven bolt loading does not affect sealing
4. What are the strengths of kammprofile gaskets?
The kammprofile gasket is our best friend for heat exchangers and other custom flanges. Kammprofiles are very hard and difficult to break during assembly, they can work under high temperature, and high pressure, and can withstand large bolt loads. Kammprofile gaskets come with the following strengths:
1) Flexible Sealing
Excellent stability allows Kammprofile gaskets to work efficiently at different seat stress levels. These gaskets provide good results whether flanges have different bolt loads or are installed incorrectly. Damage to flanges is also the smallest Kammprofile gasket because PTFE layers, graphite, silver, or aluminum are used to manufacture these gaskets. Additionally, lower seat stress minimizes gasket removal issues.
2) Chemical Resistance
Kammprofile gaskets are ideal for industrial environments where hazardous chemicals are used. The high chemical resistance and sufficient sealing stress of these gaskets ensure that the sealing function works well with machine parts in industrial plants that handle chemicals. Due to this characteristic of the gasket, chemical spills are prevented from reaching people and the environment. Therefore, on-site safety can be guaranteed in petrochemical plants, nuclear power plants, chemical plants, and other application fields.
3) Pressure and temperature resistance
Many industrial plants use pressure and temperature control during production. Kammprofile gaskets are effective sealants in manufacturing and research plants where high pressures and temperatures are the norms.
4) Reusable
For industrial users, Kammprofile gasket manufacturers can refurbish used gaskets and make them reusable when needed. Refurbished gaskets increase savings for users of these gaskets.
5) Longer Shelf life
The sturdy nature of the Kammprofile washer gives it its ability to remain effective for extended periods of time without wear. This feature reduces maintenance costs and provides additional value to the end user of the gasket. Therefore, the processing of the gasket can be avoided.
5. What are the Weaknesses of Kammprofile Gaskets?
The disadvantage of these gaskets is that they are hard and more susceptible to flange surface imperfections. Therefore, we need to ensure that our flange sealing surface has minimal dents and scratches and that it meets the flange surface flatness.
6. What are the types of Kammprofile Gaskets?
Typically, Kammprofile gaskets are available with soft components such as PTFE and graphite covering. PTFE Envelope Groove Gaskets provide the properties of PTFE materials, thereby enhancing the performance of the gasket. Types of Kammprofile gaskets currently available include grooved, metal, and corrugated metal gaskets.
Grooved Kammprofile gaskets provide better sealing performance due to their design. These gaskets can vary in size from a few millimeters to thousands of millimeters depending on the end user’s custom requirements. Due to their low failure rate, these gaskets are widely used by manufacturers all over the world. Trusted manufacturers that they will offer groove gaskets that comply with regulations.
7. What is the seating stress of Kammprofile gaskets at 70°F?
- Flexible Graphite PTFE
- Minimum: 2,900 lb/sq in
- Recommended: 13,000 lb/sq in
- Maximum: 58,000 lb/sq in
8. What are the applications of Kammprofile Gaskets in various industries?
Kammprofile gaskets are available in a variety of shapes and sizes from gasket manufacturers. As per the application, these gaskets can be custom designed. Because of the tightness and optimum performance offered by grooved gaskets, these are used as critical components in industries such as oil and gas, power plants, and nuclear installations.
- In the petrochemical and chemical industries, kammprofile gaskets are effectively used for challenging applications like environments with superheated steam or high-pressure hydrocarbon. Pipelines and heat exchangers also use these sealants.
- Pressurizers and steam generators are fitted with kammprofile gaskets in power plants. Here, they are also utilized as valve cap gaskets and heat exchanger gaskets.
Kammprofile gaskets are composite gaskets and effective sealants that provide safety in harsh conditions. For industrial applications, gasket manufacturers produce standard and custom models upon request.
9. What are the differences between Spiral-wound gaskets and Kammprofile Gaskets?
There are many differences between Spiral-wound gaskets and Kammprofile Gaskets. We can make a brief comparison of them. The differences include:
- Unlike spiral wound gaskets, all compressive forces are applied to the Cam Profile graphite face, resulting in a very tight seal. Since kammprofile is basically a solid metal, rather than alternating layers of metal and filler applied in spiral wound gaskets, it is extremely resilient and easy to handle, even at large diameters.
- Kammprofile gaskets have much less compression than spiral wound gaskets, around 0.022 inches, while spiral wound gaskets have an average compression of 0.050 inches. As a result, the kammprofile gasket loads faster, reducing the risk of non-parallel flanges.
- Price-wise, kammprofile washers are significantly more expensive. However, their increased upfront costs can be compensated by avoiding costly, unplanned outages and lost production.
- If the mating flanges are too close together, and since the graphite face is more susceptible to mechanical damage, the gasket may be vulnerable to mechanical damage or abuse during installation, a spiral wound gasket may have a small advantage. Likewise, helically wound gaskets may be more resistant to oxidation in some applications because the windings hold the graphite in place and protect it.
- On the other hand, kammprofile gaskets are more forgiving of sealing surface defects and more effective in sealing fugitive emissions in service.